Case Studies
Case studies are important as they are the only way to compare the theoretical diagnostics to the actual physical condition of the component. Case studies provide evidence that the advice given is accurate and installs confidence and trust in the service being provided.
Case Study : Collapsed Bearing
When collecting vibration data from a tail pulley bearing, it was noticed that the vibration levels had reduced significantly from the previous survey. However, the bearing was very hot. This raised alarm bells for the Howler reliability consultant and an immediate inspection revealed a collapsed bearing.
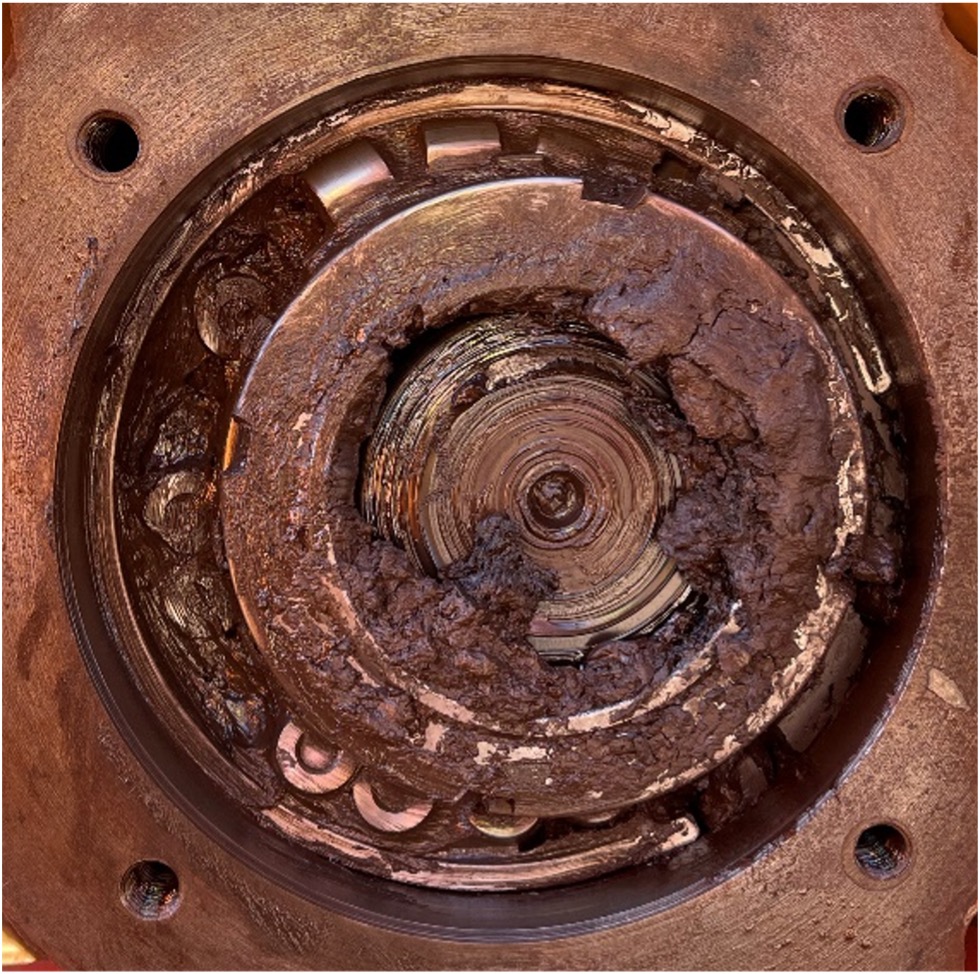
Case Study : Damage Averted
Using thermography, a Howler reliability consultant detected a worn liner in a client’s SAG Mill discharge hopper. The liner was replaced at the next scheduled shutdown preventing damage to the hopper.
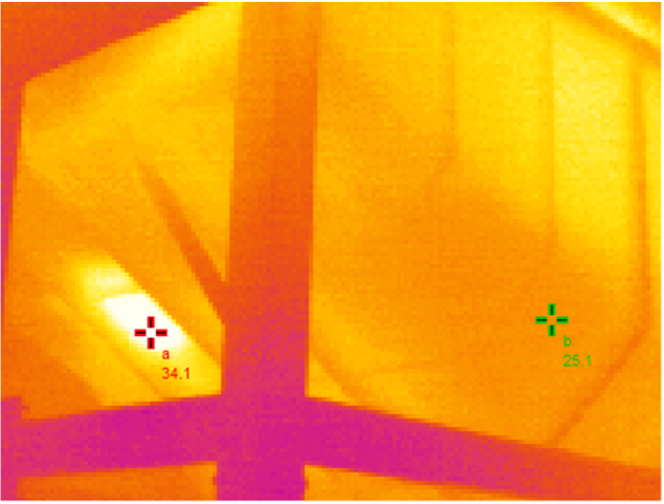
Case Study : Failure Prevented
A routine vibration survey of a client’s jaw crusher motor reviled a significant increase in impacting within the motor drive end bearing. The root cause was a rapid deterioration of an outer race bearing defect. The motor was replaced at the next shutdown and the following survey shows levels were back to normal.
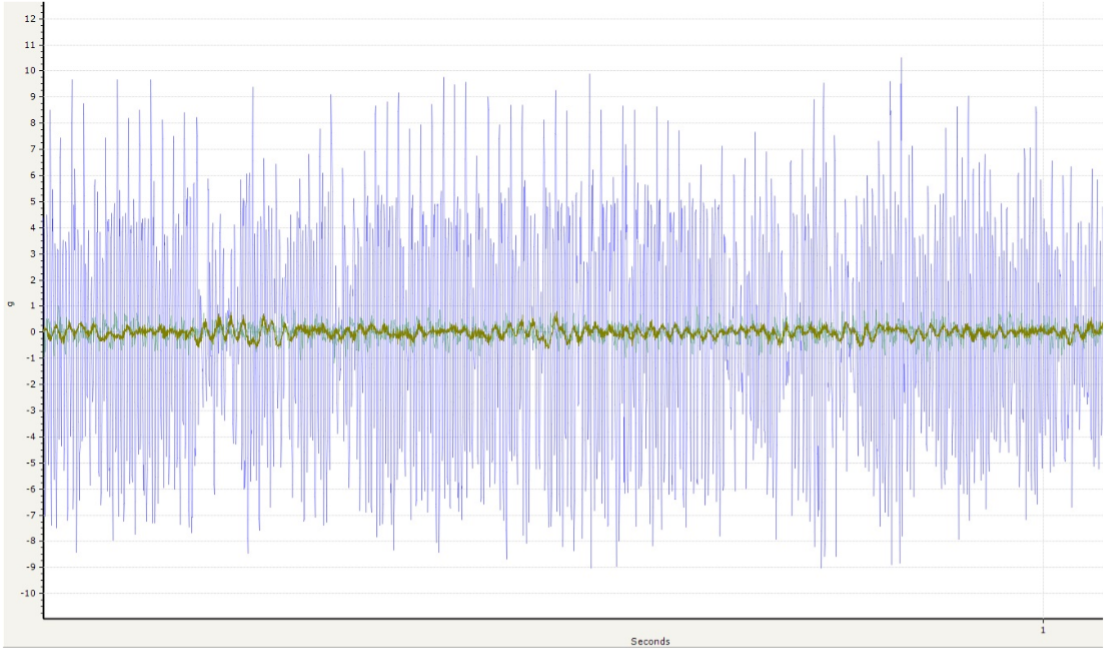
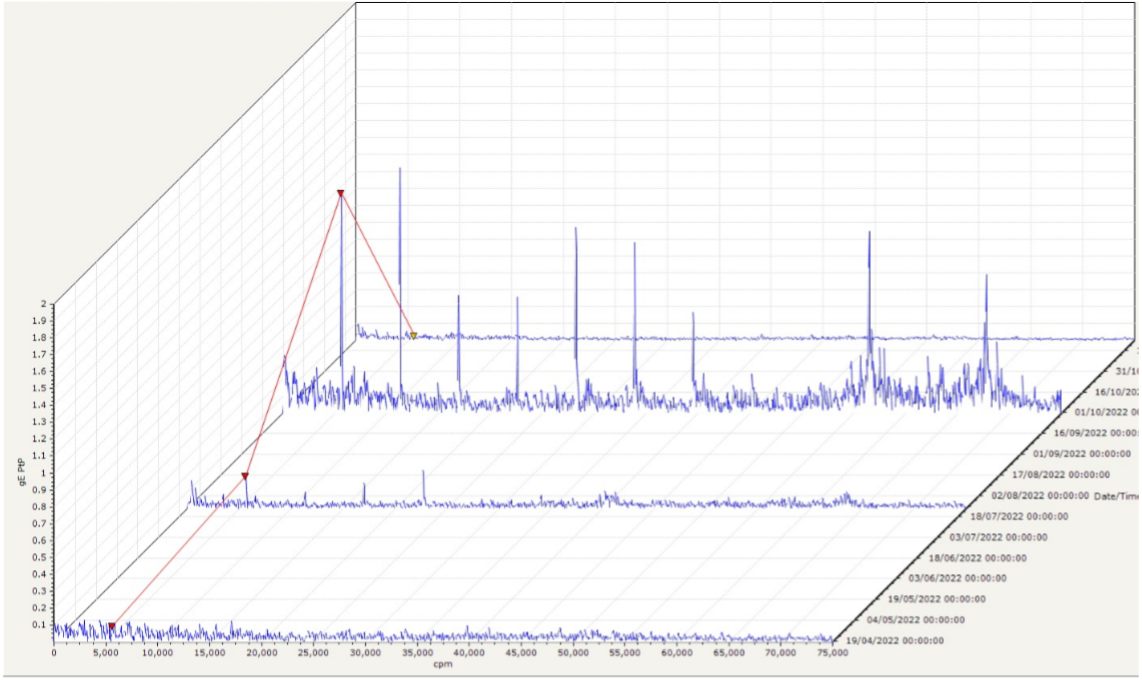
Case Study : Quick Action
When vibration data was being collected from a snub pulley bearing at a customer’s site, significant vibration could be felt throughout the entire walkway and structure.
The data showed significant impacting related to rollers skidding and a broken cage. This would have certainly resulted in a seized bearing and lost production if the defect was not identified by the Howler reliability consultant and quickly acted upon by the client.
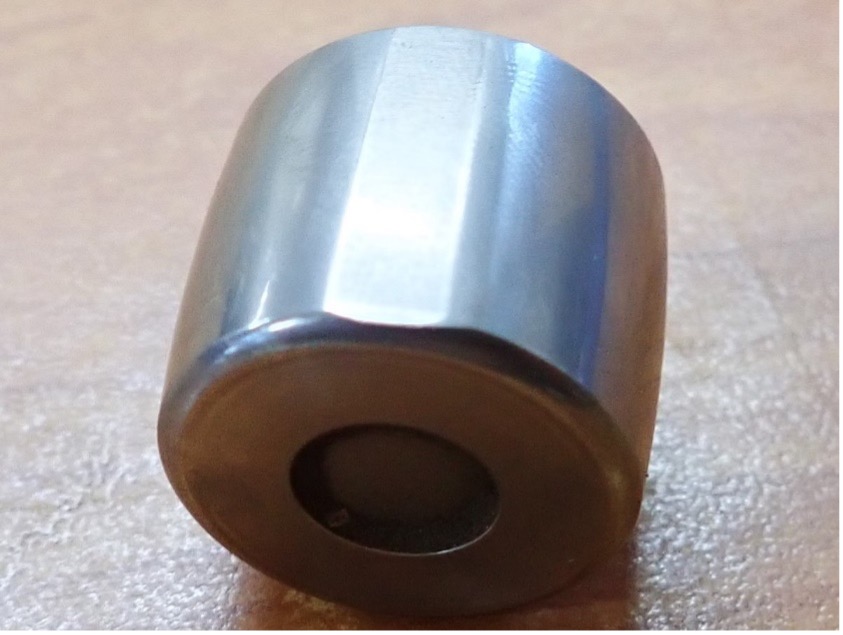